Jan 2016
Collaboration and technology
by Tom Finan, Executive Director, Construction Forum STL
When you think of too many people in one place at one time, what image comes to mind? An endless parade of clowns exiting a Volkswagen Beetle? The iconic Life magazine photograph from the 1950s that shows about a dozen college students crammed into a phone booth when “phone booth stuffing” was a craze? (The latter would assume that you’re old enough to remember both Life and phone booths.)
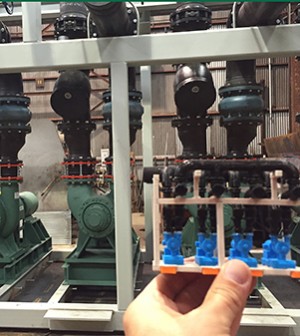
Hand (in foreground) holds a 3D model that was used to calculate lifts and placement of the 14.5-foot-high pump skids (in the background) at the BJC Kingshighway north campus penthouse site.
How about a construction site? Anyone who has been on a major project during the wrap-up stage can summon up mental images of tradespeople tripping over one another, ladders damaging finished surfaces, completed work ripped out.
The team building one of the largest projects to hit St. Louis in decades, BJC Campus Renewal Phase I, knew that on top of the usual phasing and scheduling woes, they were dealing with placing a massive building onto a postage-stamp-sized site. The entire Campus Renewal project process has embraced a marriage of collaboration and technology from the beginning.
High-Level Talks
For the mechanical penthouse atop the Barnes-Jewish north tower, multiple forms of state-of-the-art technological tools were involved. But the most powerful tool involved was collaboration of all the players, Steve Faust, business development and diversity coordinator for icon Mechanical said. “That collaboration of having everybody in the room talking made the difference,” Faust said.
“We said, let’s use this technology and collaborate on the front end.” ACW chose icon to perform the work following a competitive process with three other mechanical contractors. The scope included all work above level 13 concrete except the exterior envelope, structural concrete and interior architectural. BJC was self-procuring the cooling tower and chillers. The big kicker was that work was to start on site Dec. 1, 2015 and chilled water must be delivered by June 1 of 2016. “We knew the only solution was to begin building long before the space would be ready” Faust said.
The Big Bid Theory
Each mechanical contractor submitted their process for managing the construction of the penthouse with its pumps and other components. It was a long path to get to final selection. “We bid the job in the summer of ’14,” Dennis Savat, lead project manager for icon, said. “The design started with discussions in November 2014 and continued right up to the award. All four contractors who bid it had free reign with a certain amount of constraint.”
icon is evolving to an estimating protocol where all estimates are made from BIM models generated by the company’s in-house engineering staff. The company’s embrace of technology made it possible for the entire building team to review the impact of any proposed changes on phasing, schedule, and costs. Modularization on this project was a given. But what those modules would look like and how they would be installed in the building evolved through a combination and collaborative project management experience. The plan was to build pump skids in icon’s Granite City fabrication shop and raise them to the penthouse level by crane.
The modules needed to be no more than 14.5 feet tall in order to travel by road to the site, and no more than 40,000 lbs. in weight, so that the crane could lift them. In addition the weight had to include 3,000 – 4,000 lbs. of shackles and spreader bars in order to not max out the crane. The finished units are being put in place with only four field welds. All other prefabricated connections are flanged or grooved.
Savat said that while equipment this massive normally would be installed in pieces, the only disassembly that will be required is to remove the heads from two of the centrifugal chillers, which, “almost maxed out on weight and height.” In addition to the pump skids, there is a 70-foot-long cooling tower rack. There is 750 linear feet of 24-inch piping alone, not mention other sizes. “You don’t set that into a building that’s already in place,” Savat said. So the plan became to set the equipment, then erect the penthouse around it. The pipe skids were to be set on legs.
Once they were all in place and covered, Ben Hur would erect the penthouses’ steel frame around them. The skids would then be tied into the structural steel above with vibration isolation hangers, and the legs would be removed.
War Games
Mike Bieg, owner of icon Mechanical, invested in a 3D printer so the icon project team, like generals preparing for a battle, could move models of the assembled skids around on a floor plan grid. They calculated crane swing radii into their exercises, to see which pieces could feasibly be set in place by crane.
“There were things we couldn’t do,” Savat said. Some of the skids would need to be rolled into place. All of the lifts were scheduled to be done in a two-week period beginning Dec. 1, as soon as the deck concrete was poured. “We needed to get off the crane so Ben Hur could erect the steel,” Savat said.
By July of 2015, fabrication drawings were complete. As December neared, work that would have just been starting in the field was complete and ready to be put in place. Savat said that approximately 15,000 man hours were expended building the skids in icon’s shop. He said that shop fabrication is approximately 30 percent more efficient than field work, and estimates the total labor savings at 40 percent for this site.
icon’s Steve Faust notes that there’s another intangible savings to prefabrication. “It makes the jobsite much safer and efficient. You have improved quality, fewer crafts persons on site thereby reducing the overall general conditions.”
BJC Healthcare’s vision statement is, “The World’s Best Medicine Made Better.” By combining the latest construction technology with collaboration that leverages the experience of the entire team, the BJC Campus Renewal project team is helping to move that vision forward.
http://www.constructforstl.org/